PYROSIL® Process
Creating a nanoscale-roughness
The PYROSIL® Process is based on the flame-pyrolytic deposition of amorphous silicon dioxide on a substrate material, and thus a type of silicate coating. The surface to be treated will be fed through a gas flame which is doped with a silicon-containing precursor material (PYROSIL®). The PYROSIL®, also referred to as the precursor, burns in the flame and deposits on the surface in a very thin but dense and firmly adhering silicon oxide coating (5 – 100 nm). Due to the short flame-substrate interaction the material’s surface temperature remains moderate. Thus, the PYROSIL® Process is suitable not only for glass, ceramics or metals but also outstanding for plastics.
Structured, strongly enlarged surfaces with improved chemical bonding opportunities can be treated effectively and cost-efficiently with the PYROSIL® Process.
Coating Properties
- Roughening (nano-porous) of the material surface
- Hydrophilisation of the surface, very high surface energy
- Invisible and flexible coating
- Realization of a well-defined and highly reactive surface
- Long-term stable coating (in combination with a primer, it can be stored without activation loss for 1 – 4 weeks before further processing
Process Properties
- Effective and cost-efficient scalable process
- Low temperature protects material
- Can be used for nearly any materials
- Parameters can be customised for customer requirements
Applications
- Adhesion promotion layer for varnishes and glues
- Corrosion protection layers
- Sealing layers
- Barrier coatings
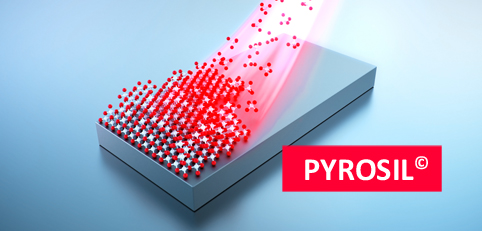
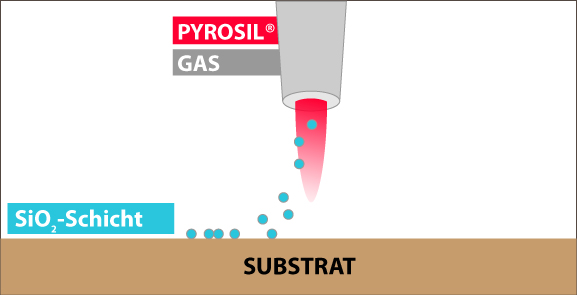
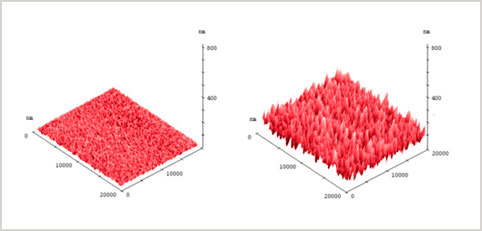
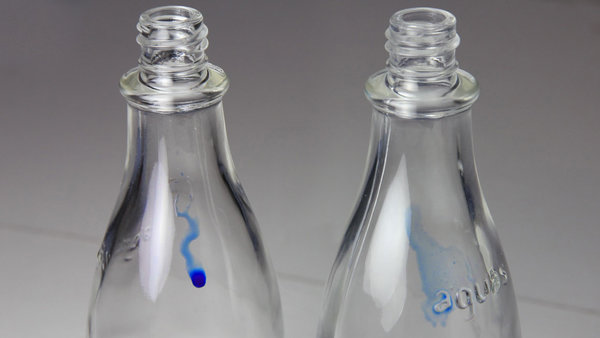
We will gladly advise you. Please contact us.
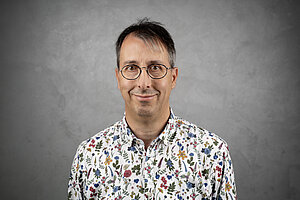
Contact person:
Dr. Norbert Eckardt
Phone: +49(0)3641 20 49 8-27
Mail: eckardt(at)sura-instruments.de